This is the standard method for installing concrete curbs. The mixture is comprised of cement(s), aggregate(s), water, and other possible chemical admixtures, such as air entrainer and pigment. When the mixture is finished, it is allowed to harden, forming a solid curb. Concrete curbs can be pigmented to match the adjacent sidewalk (See Pigmented Concrete [Dark] and Pigmented Concrete [Historic Materials]).
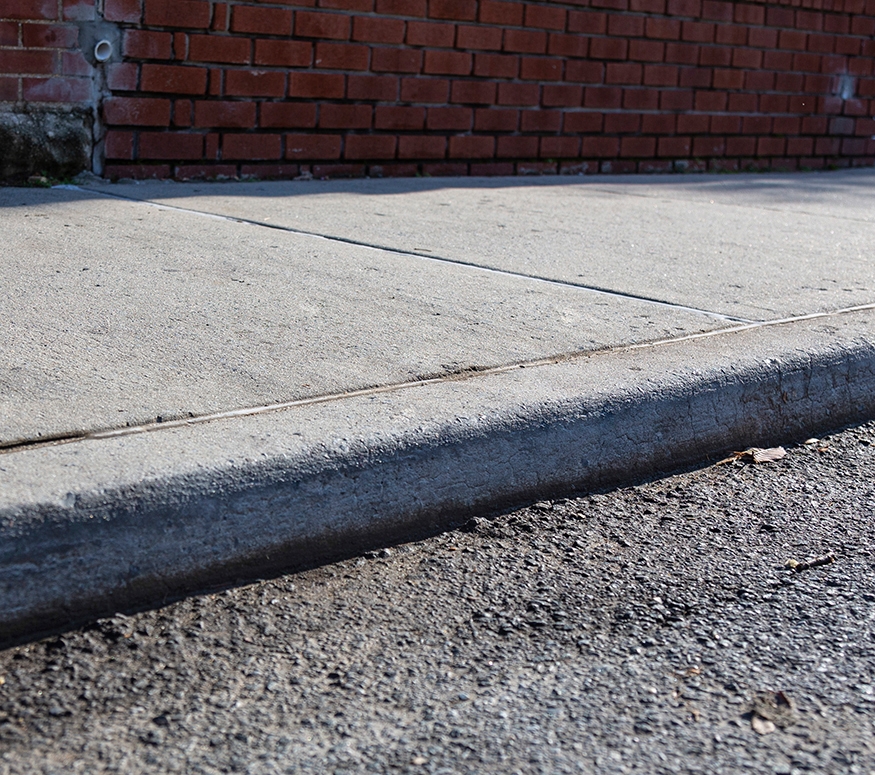
Benefits
- This material is widely available and cost-effective
- Can easily be cast on site to fit curved sidewalk profiles
- Cast-in-place curbs are more resistant to displacement than stone alternatives
Considerations
- Concrete curbs without steel facing are more vulnerable to breakage or crumbling
- Steel faced drop curbs per Standard Detail H-1015 should not be used where bike lanes cross curbs
Application
- This material is Standard for any street with Unpigmented Concrete sidewalks
Design
Concrete curb specification source: DOT Standard Specifications Section 4.08, 3.05
Steel-faced curb specification source: DOT Standard Specifications Section 2.13, 3.05, 4.09
Concrete curb detail source: DOT Standard Details drawing # H-1044
Steel-faced curb detail source: DOT Standard Details drawing # H-1010
- Size: 6 inches wide on top, 8 inches wide on bottom, 18 inches deep; 7-inch reveal above roadway
- Expansion joints of curb should line up with expansion joints of sidewalk
- Steel facing should be used on streets where repeated mounting by heavy vehicles may cause damage
- May require metal reinforcement bars as specified by DOT
- For pigmented concrete curbs, see Pigmented Concrete (Dark) and Pigmented Concrete (Historic Materials) for design guidance and
- specification information on pigmented concrete sidewalks
- Sustainability opportunity: Supplementary cementitious materials (SCM)
- Sustainability opportunity: Salvaged or recycled steel facing
Maintenance
See maintenance for Unpigmented Concrete
- DOT generally maintains this material